在电子工业中,胶粘剂不仅要实现部件的固定,更要承担 “功能传导” 的关键角色 —— 其中导电胶与导热胶是两类典型的功能性胶粘剂。尽管名字相似,但二者的核心作用、应用场景及选型逻辑截然不同。本文将拆解两者的本质差异,并分享电子工业中功能性胶粘剂的选型技巧,助力精准匹配生产需求。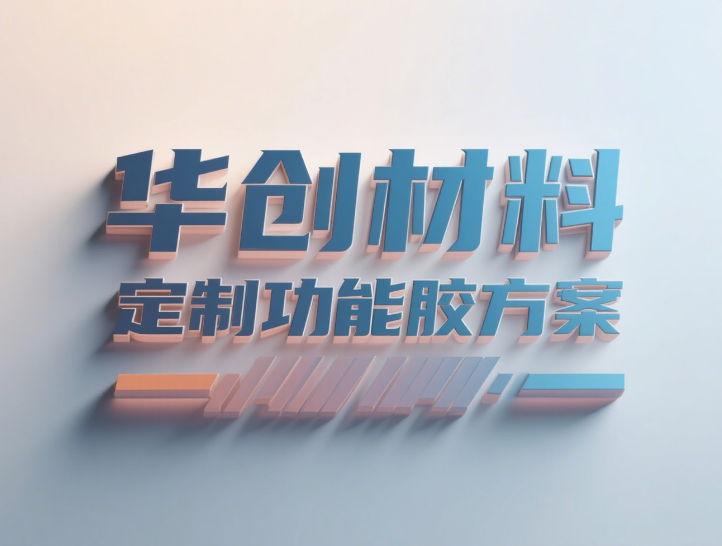
一、导电胶与导热胶:功能本质决定应用边界
1. 核心功能与成分差异
导电胶的核心使命是传导电流,其配方中需添加高导电性填料 —— 常见的有银粉(导电性最佳,成本较高)、铜粉(导电性次之,需防氧化处理)、镍粉(导电性一般,适合低成本场景)等,填料含量通常占 60%-90%,通过粒子间的紧密接触形成导电通路。此外,基胶(环氧树脂、硅橡胶等)提供粘接强度,确保导电填料在被粘物表面稳定附着。
导热胶的核心功能是传导热量,其关键成分是导热填料(如氧化铝、氮化硼、碳化硅、金属粉末等),通过填料的连续接触构建导热网络,基胶则负责粘接与绝缘(除特殊导电导热一体胶外,多数导热胶为绝缘型)。导热性能以 “导热系数” 衡量(单位 W/(m・K)),普通导热胶系数约 0.5-5W/(m・K),高导热型号可达 10W/(m・K) 以上,远高于普通胶粘剂(0.1-0.3W/(m・K))。
2. 应用场景:从 “电流路径” 到 “散热通道”
导电胶的应用聚焦于替代传统导电连接工艺,适用于无法焊接、需柔性连接或微型化的场景:
- 柔性电子领域:如柔性显示屏的电极连接、可穿戴设备的线路导通,导电胶的柔韧性可适应部件弯曲变形,避免焊接的刚性断裂风险;
- 微型电子元件:在传感器、射频模块中,导电胶可实现精密电极的 “无铅连接”,规避焊接高温对元件的损伤;
- 电磁屏蔽:通过导电胶将金属屏蔽罩与壳体粘接,形成连续导电层,阻断电磁干扰(EMI)。
导热胶则是热管理系统的 “桥梁”,用于解决电子元件与散热部件的热传导问题:
- 功率器件散热:如新能源汽车的 IGBT 模块、服务器 CPU 与散热片之间,导热胶可填充两者表面的微观缝隙(减少空气隔热层),将热量快速传导至散热部件;
- LED 灯具散热:LED 芯片工作时产生的热量需通过导热胶传递至铝基板,避免高温导致光衰或寿命缩短;
- 密封与散热一体场景:在户外电源、通讯基站的模块封装中,导热胶既能固定部件,又能通过壳体导出内部热量,同时阻断灰尘与湿气。
3. 性能指标的 “天壤之别”
| | |
| | 导热系数(越高越好,常规 0.5-10W/(m・K)) |
| 中等(优先保证导电性,剪切强度通常 5-15MPa) | 较高(需承受散热部件重量,剪切强度 8-20MPa) |
| -50℃~120℃(特殊型号可达 200℃,避免高温氧化) | |
| | |
| | |
二、电子工业功能性胶粘剂选型技巧
电子工业对胶粘剂的要求苛刻 —— 既要满足功能传导,又要适配生产工艺与使用环境。选型需围绕 “场景优先级” 展开:
1. 明确核心需求:功能优先于形式
- 若需 “导电 + 粘接”:优先看体积电阻率(如高频电路需<10⁻⁴Ω・cm),其次考虑接触电阻稳定性(避免长期使用后氧化升高);异向导电胶(仅 Z 向导电)适合精密引脚连接(如 LCD 与驱动板),可避免短路。
- 若需 “导热 + 粘接”:根据散热功率计算所需导热系数(如 10W 以上器件建议>3W/(m・K)),同时关注热阻(越低越好,需配合界面压力优化);若部件有振动(如汽车电子),选择柔性导热胶( Shore A 硬度 50-70),避免刚性开裂。
2. 适配生产工艺:效率与稳定性兼顾
- 固化方式:自动化生产线优先选单组份加热固化型(如导电胶 120℃/30 分钟固化,适配流水线烘箱);小批量或手工操作可选双组份常温固化(注意控制混合比例,避免影响导电 / 导热性能)。
- 涂胶方式:微型元件(如传感器)适合低粘度(1000-5000cps)点胶;大面积散热(如电池包)可选高粘度(10000-50000cps)刮涂,确保涂层均匀无气泡。
3. 锚定使用环境:规避失效风险
- 耐温性:高温场景(如发动机舱电子件)需选耐 200℃以上的型号(导电胶选银粉填料,导热胶选氮化硼填料);低温场景(如冷链传感器)需确保胶层不脆化(优先硅基胶体)。
- 耐环境性:潮湿环境(如户外通讯设备)需选防水型(IP67 以上),避免导电胶氧化、导热胶导热系数下降;有腐蚀环境(如化工电子仪器)需选耐化学型基胶(如环氧改性胶)。
4. 隐性需求不可忽视
- 环保合规:消费电子需通过 RoHS、REACH 认证(避免铅、镉等重金属);医疗电子需额外满足生物相容性(如 ISO 10993)。
- 长期可靠性:优先选择经过老化测试的产品(如 1000 小时 85℃/85% RH 测试后,导电胶电阻变化率<20%,导热胶导热系数下降<10%)。
三、精准选型的底层逻辑:场景化定制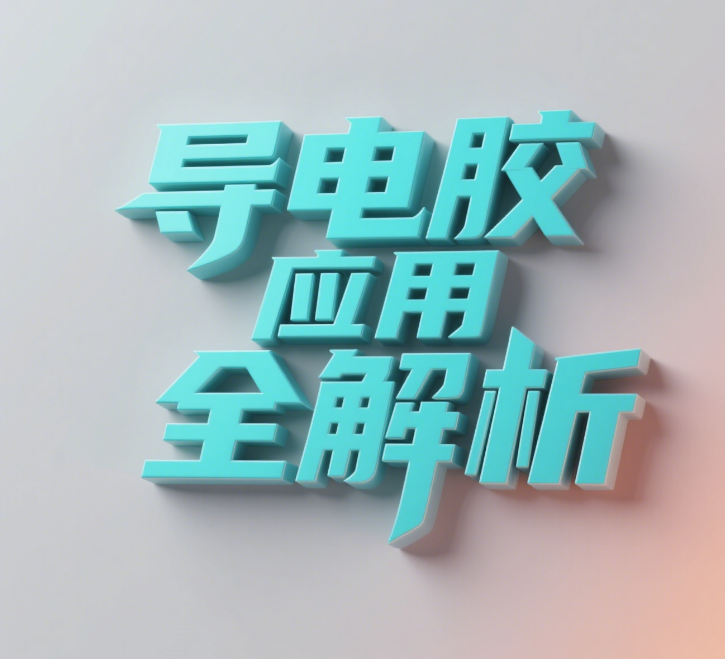
导电胶与导热胶的选型,本质是 “功能、工艺、环境” 的平衡艺术。例如,在 5G 基站的功率放大器中,需同时解决 “射频信号导电” 与 “模块散热”:导电胶需低损耗(避免信号衰减),导热胶需高导热系数(>5W/(m・K))且与铝制散热片兼容(不发生电化学腐蚀)。
华创材料等专业供应商可提供场景化解决方案 —— 通过调整填料种类(如银包铜粉降低导电胶成本)、优化基胶韧性(如硅改性环氧提升导热胶耐振动性),让功能性胶粘剂既能精准传导电流或热量,又能成为生产效率与产品可靠性的 “隐形基石”。
总之,电子工业的功能性胶粘剂选型没有 “万能款”,唯有锚定核心需求,拆解场景细节,才能让每一滴胶都发挥最大价值。