在新能源汽车和储能产业快速发展的背景下,电池 pack 作为能量存储与输出的核心单元,其安全性与可靠性直接决定了整个系统的运行风险。电池 pack 封装环节中,胶粘剂不仅需要实现电芯、模组与壳体的结构固定,更需承担防火、绝缘、散热辅助等关键功能。阻燃环氧 AB 胶凭借其独特的材料特性,在新能源电池 pack 封装中逐渐成为主流选择,其应用特性与技术优势正深刻影响着电池 pack 的设计与性能。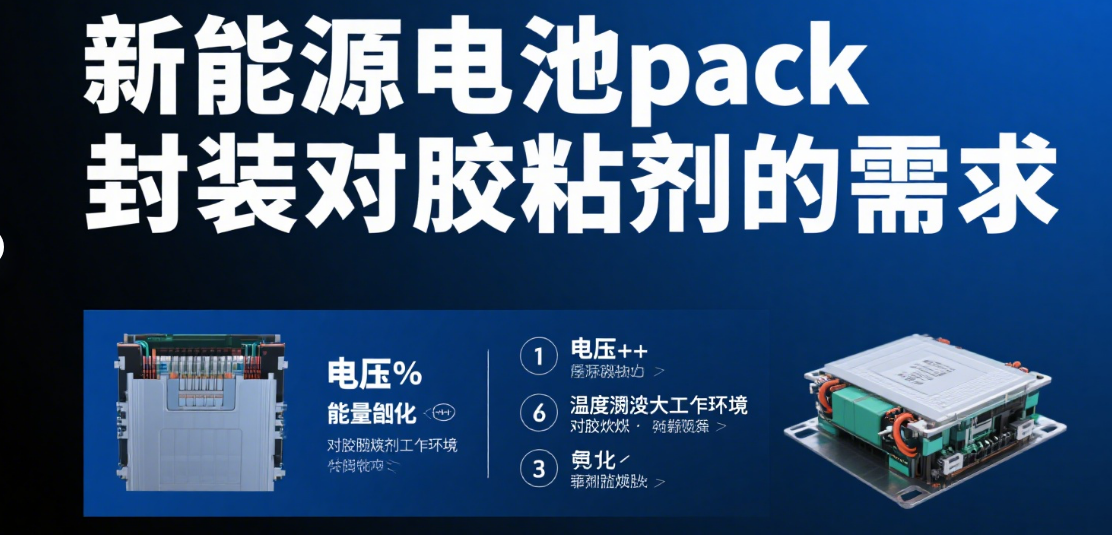
一、新能源电池 pack 封装对胶粘剂的核心需求
新能源电池 pack 的工作环境具有高电压、高能量密度、温度波动大等特点,这对封装用胶粘剂提出了严苛要求。首先,电池在充放电过程中会产生热量,极端情况下可能发生热失控,因此胶粘剂必须具备优异的阻燃性能,能延缓火势蔓延并阻隔热量传递;其次,电芯与壳体、模组间的粘结需要足够的力学强度,以抵抗车辆行驶中的振动、冲击或电池膨胀产生的内应力;此外,胶粘剂需具备良好的电绝缘性,防止电芯与金属壳体间出现漏电风险,同时需耐受电解液腐蚀、高低温循环(-40℃至 85℃)等复杂工况,确保长期稳定性。
传统封装材料如硅胶、聚氨酯胶等,虽在某些性能上满足基础需求,但在阻燃持久性、结构强度或耐化学性方面存在短板。而阻燃环氧 AB 胶通过配方优化,可同时满足阻燃、力学、耐环境等多重核心需求,成为电池 pack 封装的理想解决方案。
二、阻燃环氧 AB 胶的关键应用特性
(一)分级可控的阻燃性能,适配不同安全等级需求
阻燃环氧 AB 胶的阻燃特性通过添加磷系、氮系或磷 - 氮复合阻燃剂实现,其阻燃等级可根据电池 pack 的安全设计要求进行调控,从 UL94 V-0 级到 UL94 5VA 级不等。在电池 pack 封装中,胶层不仅需自身不燃烧,更能在高温下形成碳化层,通过物理阻隔作用延缓热量向相邻电芯的传递,为热失控预警与灭火系统响应争取时间。
例如,在三元锂电池 pack 中,由于其能量密度高、热失控风险相对较高,可选用 UL94 5VA 级阻燃环氧 AB 胶,其在 125mm 火焰垂直燃烧测试中能保持不滴落、不蔓延,且碳化层完整性良好;而磷酸铁锂电池 pack 可根据设计需求选用 UL94 V-0 级产品,在满足基础阻燃要求的同时平衡成本与工艺性。
(二)高强度粘结与结构稳定性,抵抗电池动态应力
新能源电池 pack 在使用过程中会面临多重应力:电芯充放电时的膨胀与收缩(尤其磷酸铁锂电池的体积变化率可达 3%-5%)、车辆行驶中的振动与冲击(如 ISO 16750 振动测试标准)、以及极端工况下的温度应力。阻燃环氧 AB 胶固化后形成三维网状结构,拉伸强度可达 20-30MPa,剪切强度≥15MPa,能有效将电芯、模组与壳体牢固粘结,抑制电芯位移或模组变形。
此外,其低收缩率(固化收缩率≤0.5%)可减少封装过程中的内应力集中,避免因胶层收缩导致的电芯开裂或接触不良。在动力电池 pack 的模组与下壳体粘结中,该特性可确保长期使用后胶层无脱粘、无裂纹,维持结构完整性。
(三)耐环境与耐化学性,适应电池复杂工况
电池 pack 内部环境复杂,存在电解液泄漏(如碳酸酯类溶剂)、湿度波动(冷凝水)、高低温循环等挑战。阻燃环氧 AB 胶具有优异的化学惰性,对电解液、水、酸碱性物质的耐受性强,在 85℃/85% RH 条件下经过 1000 小时老化后,粘结强度保持率仍可达 80% 以上,远高于硅胶(约 60%)。
同时,其宽温域稳定性表现突出,在 - 40℃低温下不脆化,在 120℃高温下不软化,玻璃化转变温度(Tg)可达 120℃以上,可适应电池充放电时的温度波动(正常工作温度 - 20℃至 60℃,极端情况可达 85℃),确保胶层在长期使用中不失效。
(四)良好的电绝缘性与工艺适配性
电池 pack 中,胶粘剂需隔离电芯与金属壳体、模组间的导电部件,防止短路风险。阻燃环氧 AB 胶的体积电阻率≥10¹⁴Ω・cm,击穿电压≥20kV/mm,可满足电池 pack 的绝缘要求(通常要求体积电阻率≥10¹³Ω・cm)。
在工艺适配性方面,环氧 AB 胶通过双组分混合固化,可通过自动化点胶设备实现精准涂布,混合比例(如 1:1、2:1)可根据生产线需求调整,固化时间在常温下为 30 分钟至 2 小时,加热(60℃)可缩短至 10-15 分钟,适配新能源电池 pack 的大规模量产节奏。此外,胶液流动性可调控(黏度 5000-50000mPa・s),既能填充电芯与壳体间的微小间隙(≤0.5mm),又能避免因流动性过强导致的溢胶问题。
三、相比传统封装材料的应用优势
(一)综合性能平衡更优,降低系统安全冗余成本
与硅胶相比,阻燃环氧 AB 胶的阻燃等级更高且持久性更好(硅胶长期高温下易出现阻燃剂迁移),且粘结强度是硅胶的 2-3 倍,可减少结构加固件的使用;与聚氨酯胶相比,其耐电解液腐蚀性更优,且高温下无小分子挥发物产生,避免对电池 BMS(电池管理系统)传感器造成污染。
通过 “一胶多能” 特性,阻燃环氧 AB 胶可同时实现结构粘结、阻燃、绝缘、密封等功能,减少电池 pack 内部材料种类,降低系统集成复杂度与成本。
(二)助力电池 pack 轻量化与空间利用率提升
新能源汽车对续航里程的追求推动电池 pack 向轻量化、高密度方向发展。阻燃环氧 AB 胶的密度约为 1.2-1.4g/cm³,低于金属紧固件(如螺栓,密度 7.8g/cm³),且通过粘结替代机械连接,可减少壳体厚度(如铝合金壳体厚度可从 2mm 减至 1.5mm),实现 pack 减重 5%-8%。
同时,胶层可均匀填充不规则间隙,无需预留螺栓孔等空间,使电芯排布更紧凑,电池 pack 能量密度提升 3%-5%,间接提升车辆续航能力。
(三)提升电池 pack 的热失控防护层级
在电池热失控测试中,阻燃环氧 AB 胶的碳化层可延缓热量传递速度达 30%-50%,为电池 pack 的热管理系统(如液冷板)和灭火装置争取响应时间。某新能源车企测试数据显示,采用阻燃环氧 AB 胶封装的电池 pack,在单电芯热失控后,相邻电芯发生热失控的时间延迟至 15 分钟以上,远高于行业平均的 8 分钟,为乘员逃生和系统断电争取了关键窗口。
四、实际应用案例与未来发展方向
目前,阻燃环氧 AB 胶已广泛应用于新能源汽车动力电池(如比亚迪刀片电池 pack、宁德时代 CTP 电池包)、储能电池(如阳光电源储能系统)等场景。在某款纯电动 SUV 的电池 pack 封装中,通过选用 UL94 5VA 级阻燃环氧 AB 胶,电池系统通过了针刺、挤压、热失控等国标测试,且整包重量降低 7.2kg,续航里程提升约 15km。
未来,随着电池能量密度的进一步提升,阻燃环氧 AB 胶将向低烟无卤化(减少有毒气体释放)、快速固化(适应 60 秒内量产节拍)、导热阻燃一体化(添加石墨烯等导热填料,兼顾散热与阻燃)方向发展,为新能源电池 pack 的安全与性能升级提供更有力的材料支撑。